- All Posts
- What is Offsite Manufacturing? The Future of Construction Efficiency and Innovation
What is Offsite Manufacturing? The Future of Construction Efficiency and Innovation
How Prefabrication and Modular Construction are Transforming the AEC Industry
McKinstry has been a leader in the built environment focusing on delivering integrated services and deep market expertise for more than 60 years. We provide tailored solutions to customers that prioritize efficiency and sustainability in the ever-changing market. As the industry has changed and evolved, customers are now, more than ever, seeking full-service experts to provide solutions in a more customized and efficient manner. At McKinstry, we have added a new offering of Offsite Manufacturing to meet these demands and launch our customers into the next generation of construction.
What is Offsite Manufacturing (OSM)?
Offsite Manufacturing (OSM) is a game-changer in construction, combining efficiency, sustainability and quality. However, understanding what OSM is—and what it isn’t—is crucial for leveraging its full potential.
Offsite Manufacturing (OSM) is transforming the construction industry by addressing inefficiencies and setting new benchmarks for quality, sustainability and scalability. By shifting production of larger building component segments to controlled factory environments and assembling them on-site, OSM eliminates many of the challenges associated with traditional construction methods. This approach represents a fundamental rethinking of how buildings are designed, produced, procured and delivered, offering a smarter, faster and greener way to construct the spaces of tomorrow while maintaining the customization and quality customers expect.
The Core of Offsite Manufacturing
At its core, OSM involves manufacturing components, or entire modules, in a controlled environment and transporting them to a construction site for assembly. This process streamlines construction timelines, reduces risks and improves outcomes in ways that conventional methods cannot achieve. With its ability to integrate advanced planning, engineering, and production, OSM ensures that a larger portion of the building construction is optimized for efficiency and performance.
Unlike traditional construction, which often faces delays due to labor shortages, weather conditions, and logistical challenges, OSM allows for simultaneous on-site and off-site activities. This parallel workflow can significantly reduce project timelines and enhance cost efficiency while eliminating trade stacking. This precision offered by factory-controlled environments ensures consistent quality, with advanced technologies such as automation and robotics enhancing reliability and minimizing variability. By creating components in a controlled setting, manufacturers can adhere to exacting specifications and ensure that each element meets rigorous quality standards.
One of the most compelling aspects of OSM is its alignment with sustainability goals. The process minimizes material waste, with studies showing that offsite production can reduce construction waste by an average of 78.8%. Additionally, the reduction in on-site activities decreases the carbon footprint associated with construction projects. By shifting much of the building process to a controlled factory environment, offsite manufacturing minimizes the need for heavy machinery, large labor crews, and extended project timelines at the construction site. This results in fewer transportation requirements for workers and materials, reduced energy consumption on-site, and less waste generation. Additionally, precision engineering and advanced fabrication techniques optimize material usage, further decreasing emissions and resource depletion.
With fewer deliveries, less idling equipment and a more efficient workflow, offsite manufacturing contributes to a greener, more sustainable built environment—helping organizations meet carbon reduction goals while delivering high-quality, scalable solutions.
These advantages make OSM an ideal choice for organizations seeking to reduce their environmental impact while delivering high-quality structures.
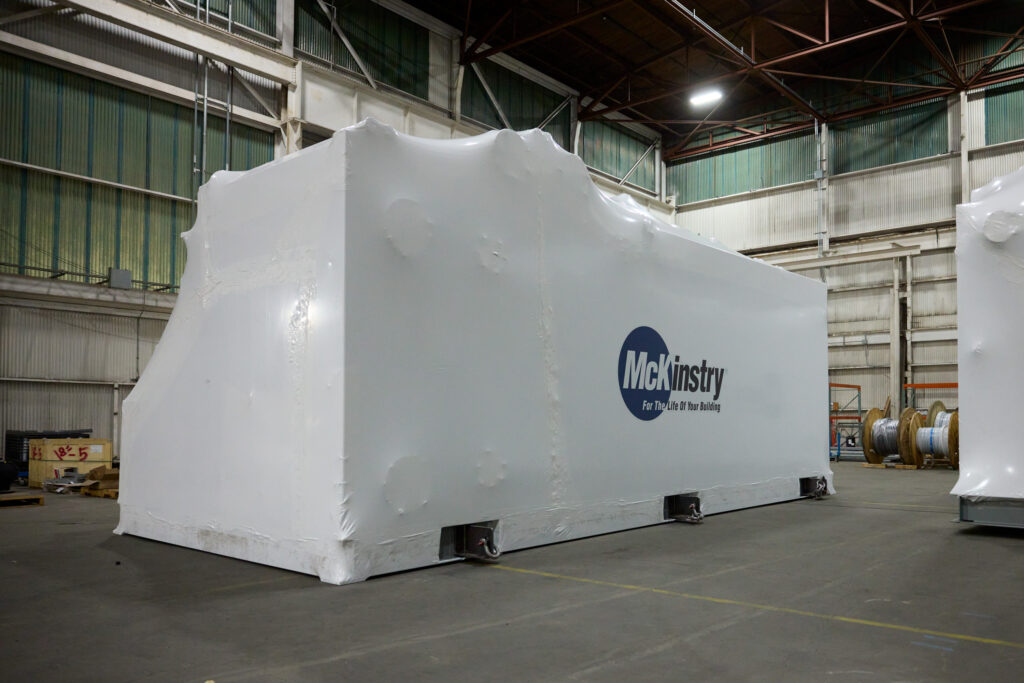
The adaptability and scalability of OSM are key to its growing adoption across industries. Modular systems allow for rapid scaling to meet demand without compromising quality or disrupting ongoing operations. Customizable designs enable OSM to accommodate diverse needs, from residential housing and commercial spaces to healthcare facilities and infrastructure projects. This flexibility ensures that structures built using OSM can evolve with changing requirements, future-proofing investments and providing long-term value.
To fully realize the benefits of OSM, it is essential to move beyond common misconceptions. OSM is not simply about prefabrication or quick assembly; it is a holistic approach that integrates design, production, and assembly into a seamless workflow. This integration enables OSM to deliver comprehensive solutions that address both immediate construction needs and long-term operational requirements.
The success of OSM lies in its ability to incorporate advanced capabilities at every stage of the construction process. For example, mechanical, electrical, and plumbing (MEP) systems can be pre-installed within modules during manufacturing, ensuring seamless integration and reducing installation time. These systems are then tested in the factory to reduce the amount of commissioning work required on-site. Structural components are designed for strength and adaptability, meeting local building codes and environmental conditions. These innovations not only enhance the efficiency of construction but also improve the performance and sustainability of completed structures.
The potential of OSM extends far beyond individual projects. Its applications span multiple sectors, including residential, commercial, healthcare and infrastructure development. Modular hospitals and clinics can be deployed rapidly in response to urgent needs, while prefabricated bridges and tunnels offer durable and efficient solutions for large-scale infrastructure projects. This versatility makes OSM a strategic choice for addressing diverse construction challenges and opportunities.
However, adopting OSM requires a shift in mindset and strategy. Early-stage collaboration among architects, engineers, and manufacturers is critical to ensuring seamless alignment throughout the project lifecycle. Robust logistics planning is essential for transporting modules and optimizing on-site assembly, while proactive engagement with regulatory requirements can mitigate delays and ensure compliance. By addressing these considerations, organizations and governments can maximize the value of OSM and achieve superior outcomes.
Offsite Manufacturing represents a big step forward in the evolution of the construction industry. Its ability to combine speed, quality and sustainability positions it as a game-changer for the built environment. As industries face increasing pressure to deliver smarter, greener, and faster solutions, OSM provides a clear roadmap for meeting these demands. By embracing its transformative potential, organizations can build structures that are resilient, adaptable, and environmentally responsible, ensuring they are well-prepared to thrive in an era of rapid change and innovation.
Explore Other News
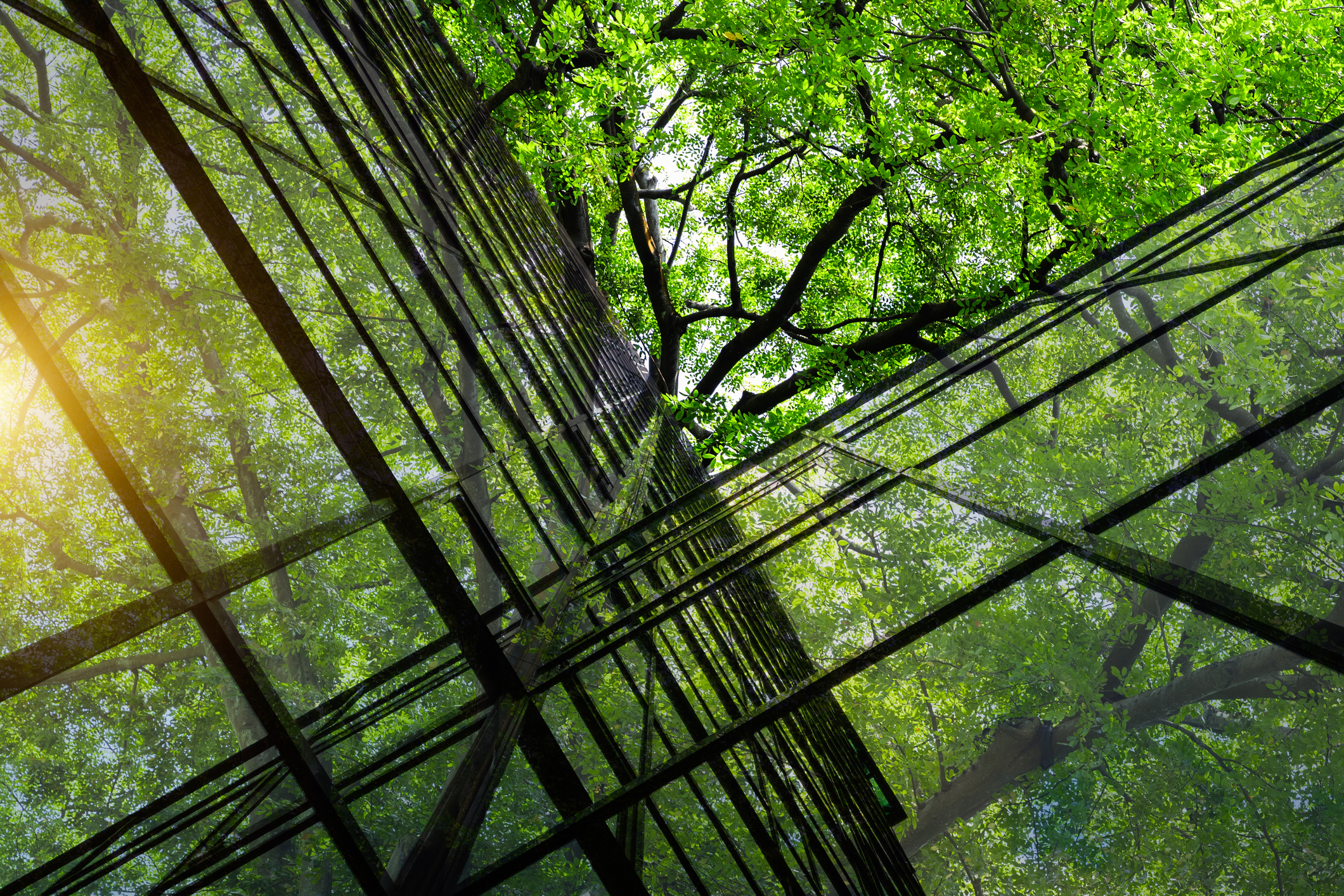
Earth Day: Collective Progress Through Common Ground
By Ash Awad, President and Chief Market Officer Each year, the lead up to Earth Day on April 22 provides an ideal …
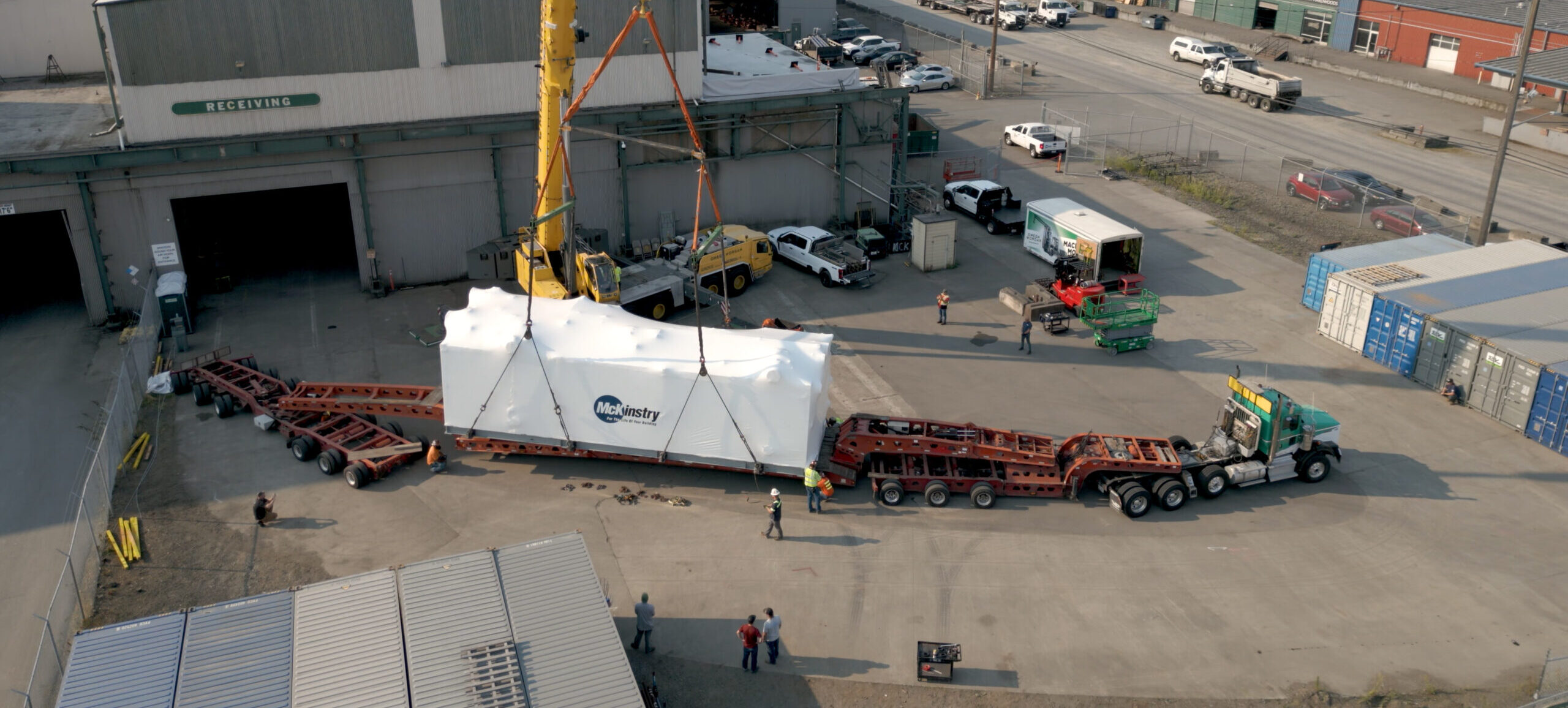
What is Offsite Manufacturing? The Future of Construction…
How Prefabrication and Modular Construction are Transforming the AEC Industry McKinstry has been a leader in the b…
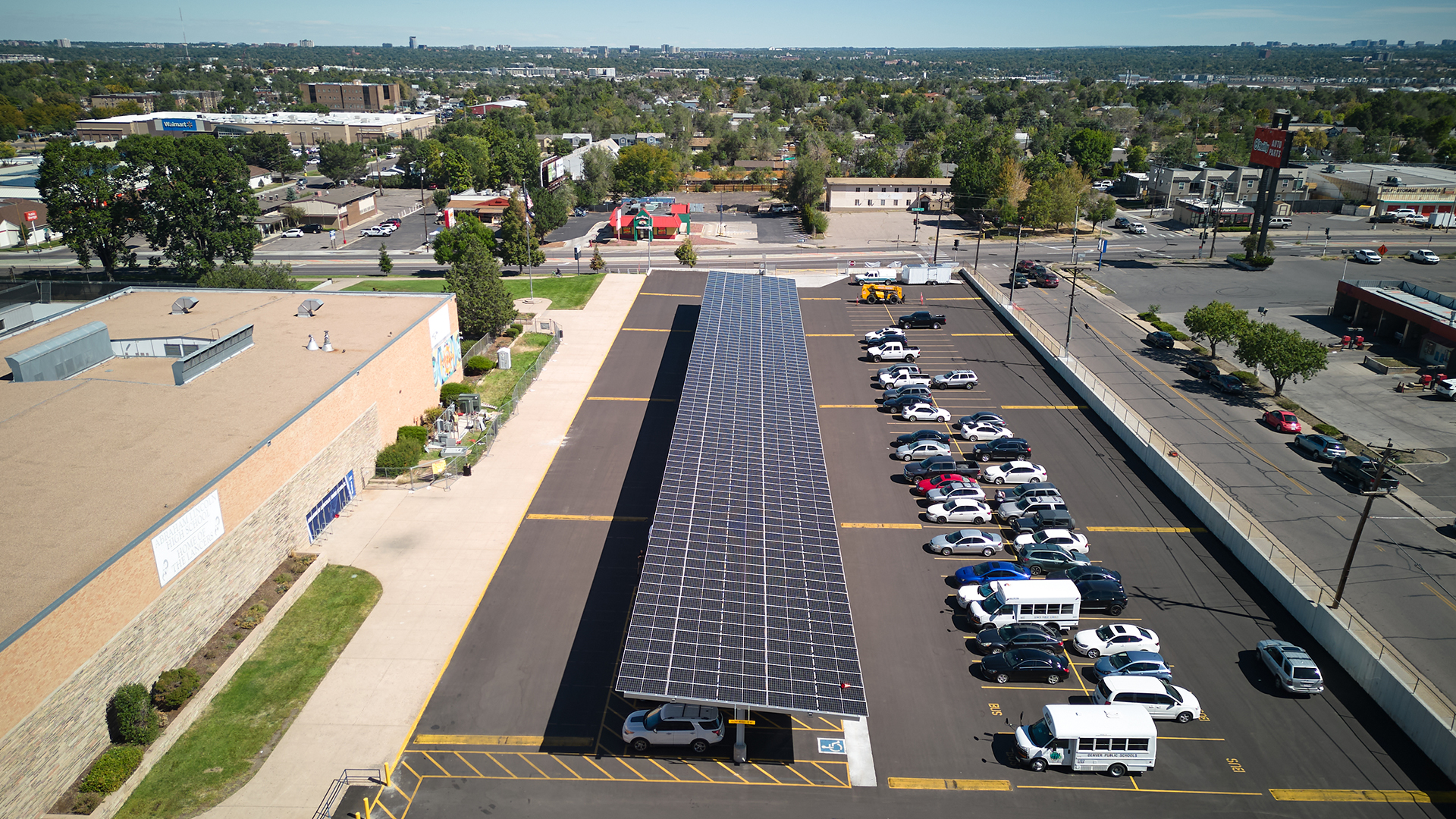
Denver Community Solar Garden: Abraham Lincoln High School
The City and County of Denver recently unveiled its new community solar garden in partnership with Denver Public Scho…